At present, the peanut shelling machine can be basically divided into steel rods for attacking and kneading, such as steel grating bars, and rubber rollers for squeezing and kneading. There are two major types of rubber floating concave plates, but the shelling quality is poor, and the damage rate is greater than 8%. The shelled peanuts can only be used for oil extraction and edible, which cannot meet the requirements of foreign trade export and seed production. The currently widely used principles of mechanical shelling of peanuts are as follows:
Shelling by Impact method: peanut is suddenly blocked at high speed and receives impact force, which breaks the shell and achieves the purpose of shelling. Its typical equipment is a centrifugal peanut sheller consisting of a high-speed rotary thrower and a rough wall plate fixed around the thrower. The throwing disc causes the peanut pod to produce a large centrifugal force to hit the wall. As long as the impact force is large enough, the pod shell will have a large deformation and cracks will be formed. When the pod leaves the wall, the shell has different elastic speeds and different movement speeds. The pods receive less elastic force and the movement speed is not as good as the shell, which prevents the shell from moving rapidly outward and cracks. To achieve hulling of the peanut kernels. The impact shelling method is suitable for pods with a small binding force between kernels, a large kernel shell gap and a relatively brittle shell. The factors that affect the hulling quality of the centrifugal sheller are the moisture content of the grain, the rotation speed of the throwing tray, and the structural characteristics of the throwing tray.
Peanut Shelling by Grinding: Peanut pods are strongly crushed between the fixed abrasive pad and the moving abrasive pad, causing the outer shell of the pod to tear to achieve hulling. The typical equipment is a disc sheller consisting of a fixed disc and a rotating disc. The pod enters the gap between the fixed grinding plate and the moving grinding plate through the feeding port. The centrifugal force of the rotating grinding plate makes the seeds move radially outward, and also causes the pod and the fixed grinding plate to generate friction forces in the opposite direction. The teeth on the sheet continuously cut the shell, and under the combined effect of friction and shear force, the shell cracks until it breaks, and detaches from the shell kernel to achieve the purpose of shelling. The influencing factors of this method include the moisture content of the pods, the straight length of the disc, the speed of rotation, the size of the working gap between the grinding pads, the shape of the grooves on the grinding pads, and the uniformity of the pods.
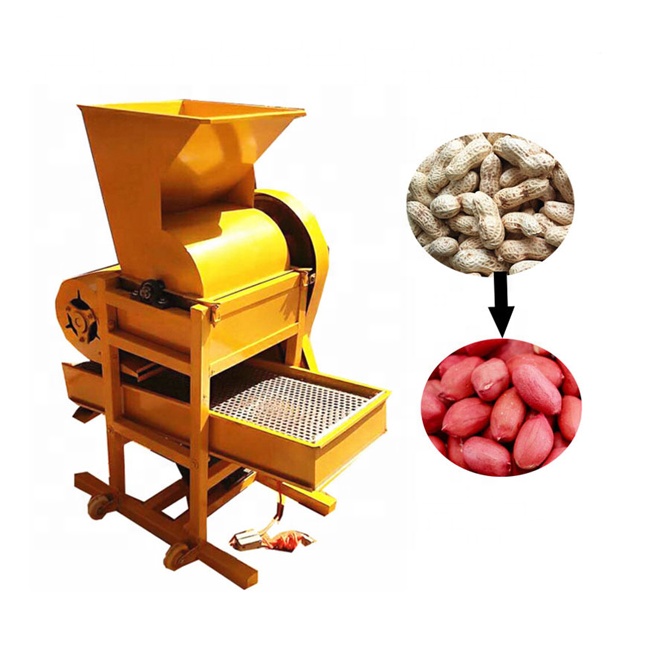
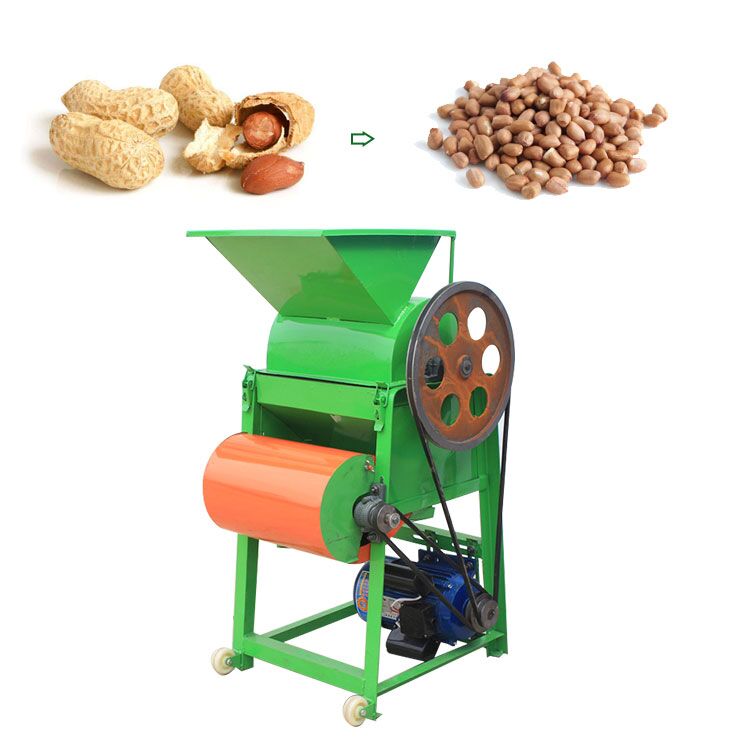
Shelling by Shearing: Peanut pods are subjected to the shearing force of a relatively moving knife plate between the fixed knife holder and the drum. The shell is cut and opened to separate the shell from the kernel. Its typical equipment is a blade shelling machine with blade drum and blade base as its main working parts. A knife plate is installed on the knife plate drum and the knife plate seat. The knife plate seat is concave and has an adjusting mechanism. The gap between the knife plate seat and the knife plate drum can be adjusted according to the size of the peanut pod. When the blade drum rotates, a shearing effect occurs between the blade and the blade, causing the material shell to rupture and fall off. It is mainly used for husking of cottonseeds, especially cottonseeds with velvet. The husking effect is better. Due to its small working surface, the phenomenon of seed leakage is prone to occur and the rate of repeeling is high. The influencing factors of this method include the moisture content of the raw materials, the height of the rotating speed of the drum, and the size of the gap between the blades.
Hulling by Extrusion Method: Hulling by extrusion method relies on a pair of cylindrical rollers with the same diameter and opposite rotation directions and the same rotation speed, adjusted to an appropriate gap, so that the peanut pods are squeezed by the rollers to break the shell. Whether the pod can smoothly enter the gap between the two squeeze rolls depends on the condition of the squeeze rolls and the contact with the pods. In order for the pod to be squeezed to break the shell between the two squeeze rolls, the pod must first be clamped and then rolled into the gap between the two rolls. The size of the gap between the two squeeze rolls is an important factor affecting the level of kernel breakage and hulling.
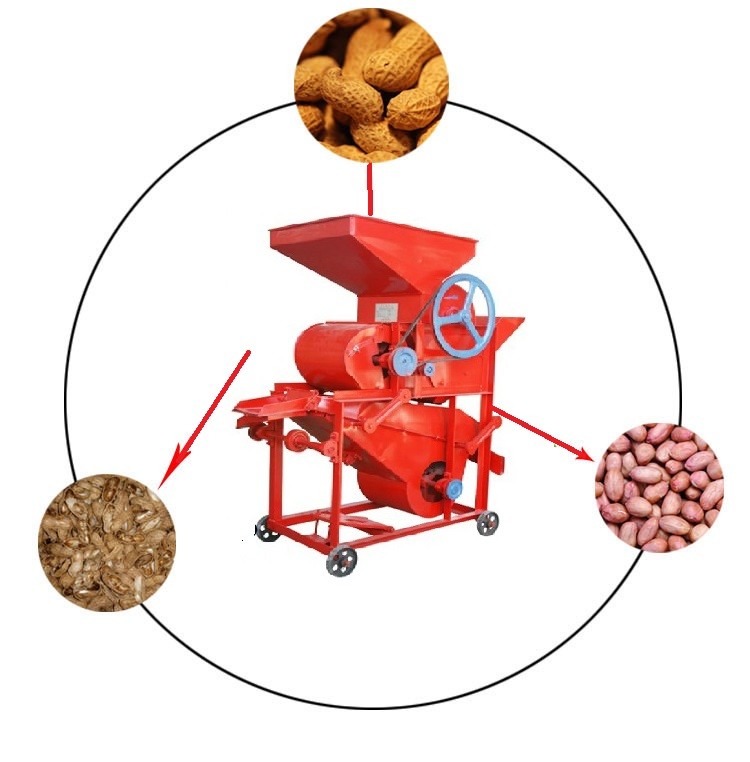
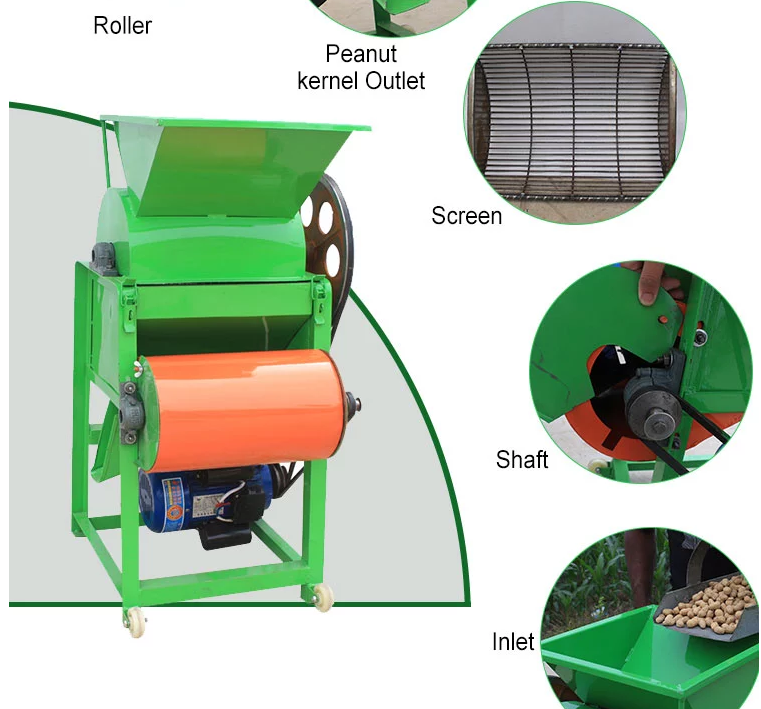
Husking by Rubbing: Rubbing and husking is the use of relatively rotating rubber rollers for rubbing and husking of the kernels. The two rubber rollers are placed horizontally and rotated at different speeds respectively. There is a certain linear speed difference between the roller surfaces. The rubber rollers have a certain elasticity. Its friction coefficient is large. When the peanut pod enters the working area of the rubber roller, it comes into contact with the two roller surfaces. If the pod meets the conditions of being pinched by the roller, that is, the angle of the rodent is smaller than the friction angle, it can enter the two rollers smoothly. At this time, the pod is pulled by the friction force of two different directions while being pulled between the rollers; in addition, the pod is also subjected to the normal pressing force of the two roller surfaces, and when the pod reaches the vicinity of the center line of the roller At this time, the normal squeezing force is the largest, and the pod is compressed to produce elasticity—plastic deformation. At this time, the pod’s shell will also rupture under the action of compression, and the hulling process is completed under the action of the above-mentioned opposite direction tearing force. Factors affecting hulling performance include line speed difference, rubber roll hardness, roll-in angle, roll radius, gap between rolls, etc.